The importance of Environmental Monitoring Programs in the COVID-19 context
The food industry, in general, is important in any country, not only providing food to the public but contributing to the economy. All organisations throughout the supply chain are responsible to provide safe, quality, and nutritious food and must adhere to strict rules and requirements that include legal and customer requirements.
The food industry however also faces many challenges that could result in products not conforming to specifications – posing a possible public health risk.
These challenges include:
- Climate change
- Outbreaks/pandemics
- Lack of communication between stakeholders
- Potential for food fraud
- Economic and political instability
- Higher demand for food
- Low maturity of food safety culture
- The potential of cross-contamination during production, etc.
With regard to the potential of cross-contamination during production, food handlers and manufacturers are required to implement effective measures to minimize or prevent cross-contamination and to establish and implement formal Food Safety Management Systems (FSMS).
FSMS are dependent on accurate identification of Food Safety Hazards and the effective implementation of control measures, i.e. Pre-Requisite Programs (PRP’s). In addition to the control of hazards, those responsible for managing the FSMS must monitor and verify the effectiveness of the control measures.
An Environmental Monitoring Programme (EMP) is a tool that can be used to:
- Provide an efficient proactive risk reduction tool (“seek and destroy”). It should be considered a ‘‘win’’ when environmental samples test positive during routine monitoring
- Conduct an in-depth investigational sampling when the routine program indicates a problem
- Verify the effectiveness of sanitation, sanitary design, employee practices, and other Good Manufacturing Practices
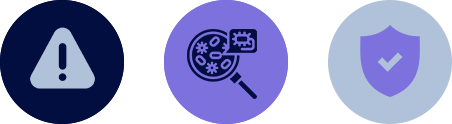
An EMP is not meant to be a checklist but a roadmap to controlling pathogens in food manufacturing sites. An investigational approach that includes a root cause analysis and corrective actions is key.
Key elements of an EMP:
- Sampling Zones
- Risk Assessment
- Sampling plan
- Corrective Actions
- Data Management
Sampling Zones
Sampling zones are areas within the manufacturing plant that are categorized according to their proximity to the product and differing levels of risk of product contamination. Pathogens to include in a sampling plan should be those that are specific for food matrix and production.
Movement of people, equipment, and materials, as well as the age of the plant and sanitation programs, all need to be reviewed over time. Each hygienic zone may have different tests and risks associated. The number and frequency of the tests may vary.
There are four (4) Sampling Zones; i.e. Zone 1, 2, 3 and 4
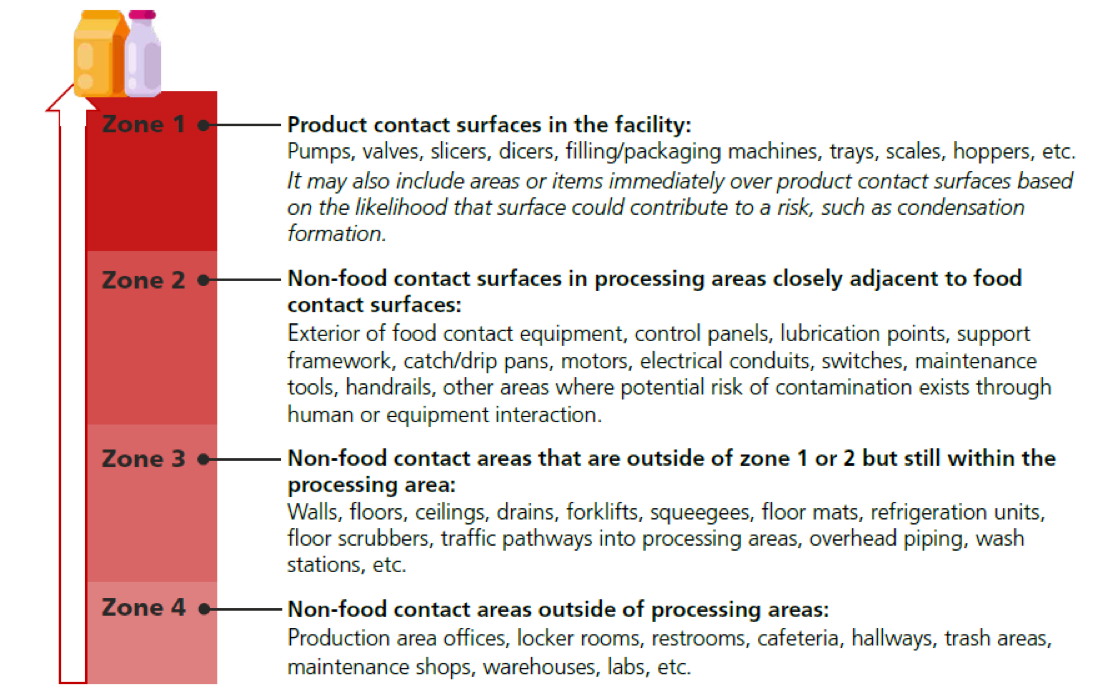
Risk Assessment
A Risk Assessment should be conducted, regardless of the size of the facility, which will provide information to assist the organisation in determining whether an EMP is needed (see Flow Diagram). Where an EMP is required, the outcome of the Risk Assessment will also provide information to establish a sampling plan. The Risk Assessment can be conducted by a multi-disciplinary team and consists of Maintenance, Sanitation, Quality Assurance/Quality Control (QA/QC), Production, and Engineering.
The outcome of the Risk Assessment will assist in identifying key areas and potential routes of contamination.
Aspects to take into consideration include:
- Traffic patterns (staff, product, waste, contractors, forklifts, tools, etc.)
- Water/condensation
- Poor cleaning practices
- Gaps in floors, porous floor materials
- Smells (bad smell can indicate general hygiene problems also allowing/facilitating pathogen entries)
- Cracks / bad infrastructure (cracks in columns can allow for water rinsing down & spreading contaminations)
- Emergency Doors / Roof Access
- Product exposure – lines open to the room
- General access (doors/hatches between different processing areas)
- Drains
- Footbridges/stair
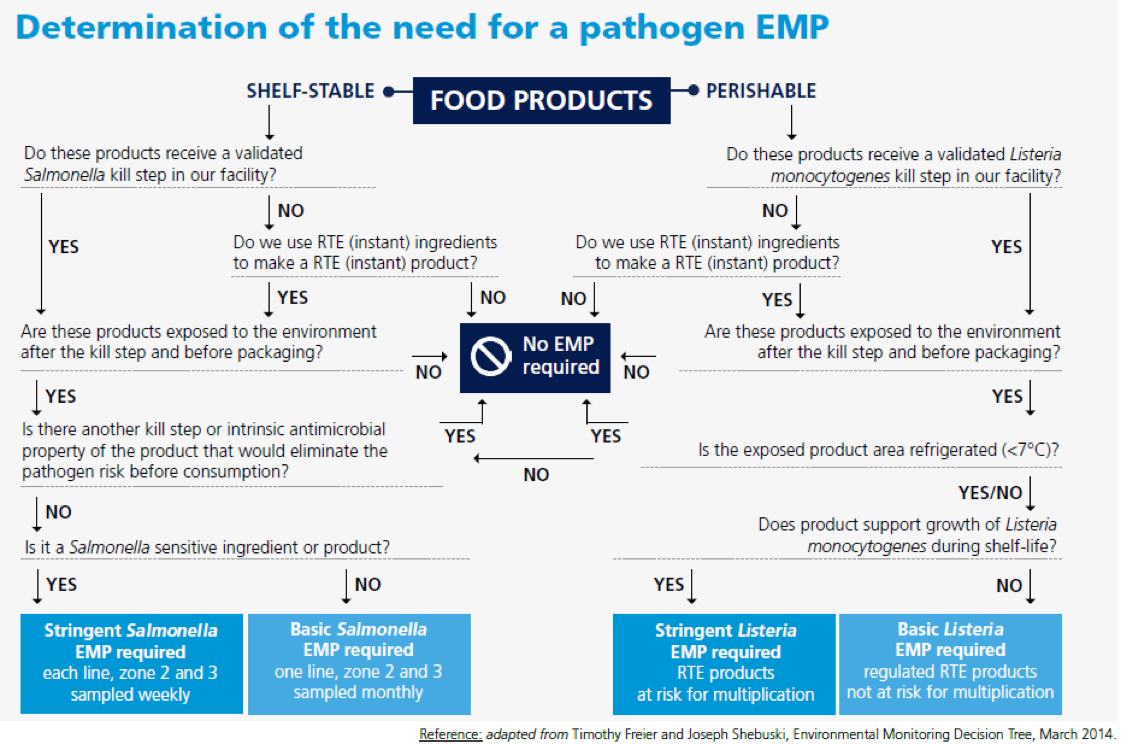
Sampling Plan
The outcome of the Risk Assessment and review of historical data (e.g. positive testing results from the past) results in the identification of most relevant sampling points to establish and implement a sampling plan that includes:
- Sample locations (documented on-site/production area plan)
- Sampling frequency
- Type of sampling (swabs, air plates, etc.)
- Sampling size
- Target organisms (pathogens, indicator organisms, etc.)
- Acceptable limits
- Sampling equipment & technique (Independent, competent, aseptic)
- Test methods
- Test laboratory
- Responsible persons (performing sampling, evaluating/analysing results, corrective actions)
- Corrective Action procedures
Corrective Actions
Establish a documented procedure for the handling of out of spec results.
Procedure to include:
- Responsible person for initiating and implementing corrective action
- Who must be informed and contacted
- A risk assessment completed based on unsatisfactory result vs product risk
- Root cause analysis investigation (see table below for possible causes)
- Corrective action defined, agreed and carried out
- Any actions and repeat analysis captured and documented
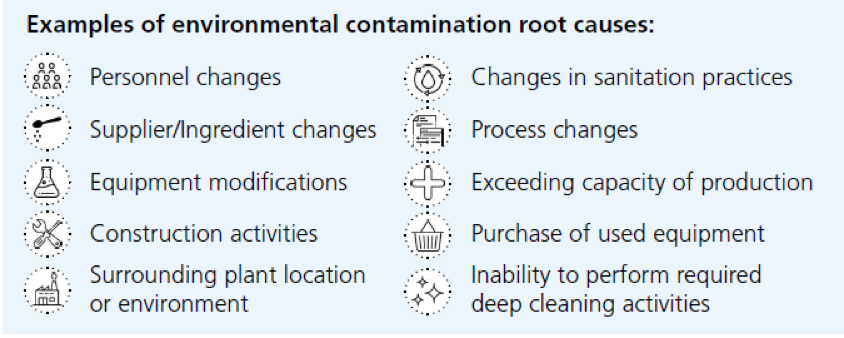
Data Management
Proper data management is key for the success of an EMP, and to have real-time actions in case of positive results and relevant long term improvements.
Exhaustive data gathering
- Each sampling point should be very carefully defined and registered
- Circumstances of sampling should be documented
- Key information to capture:
- Room, equipment, surface, zoning area (1, 2, 3, 4…), day, hour, the status of the surface (after cleaning, in process…), the status of the equipment (stopped, dismantled…), specific risk factor (after maintenance intervention…), who did the sampling, how the sampling was done (swabbing with a sponge…)
Regular data analysis
- Systematic trend analysis is required to assess a loss of control or recurrence of contamination
- Need for predefined target values and mitigation plans in case of non-conformities
In conclusion, Key Takeaways:
- Risk assessment is key in initial steps of EMP development
- Historical data are is an important source of information
- Any high risk positive should lead to an investigational control plan involving all departments to facilitate proper root cause analysis
- Zero positive over years means either perfect hygiene or, more probably, an insufficient EMP
- Data management is key for effective ‘‘seek and destroy approach‘‘
In addition, managing and monitoring the effectiveness of an EMP is important to identify opportunities for improvement. Regular reviews are required, as is staying up to date with current trends.Get in touch with our Technical Specialists for assistance with any of the EMP-related services below:
- Assistance with the implementation or review of client-specific Environmental Monitoring Programmes
- Sampling:
- Surface
- Air
- Product
- Problem-solving
- Root cause analysis performed for non-conforming performances/results through inspection and strategic sampling to identify the source of the problem.
- Corrective actions recommend how to resolve the problem.
- Training
- Sampling techniques
- Developing an EMP
EnviroMap – Environmental Monitoring Software

EnviroMap是一个基于云的安全系统,可让您自动执行环境监控程序并协助整个采样生命周期。EnviroMap在工厂地图上清晰显示,是同类最佳的解决方案,可为您的业务带来巨大收益,从而解决您的问题。

References
- http://www.fao.org/uploads/media/Codex_2004_sampling_CAC_GL_50.pdf
- http://www.fao.org/fao-who-codexalimentarius/codex-texts/guidelines/en/
- https://www.fda.gov/sampling-plans
- https://www.fda.gov/media/102633/download
- https://ec.europa.eu/food/safety/international_affairs/standard_setting_bodies/codex/ccmas_en
- Timothy Freier and Joseph Sebuski; Environmental Monitoring Decision Tree, March 2014
- Article: ‘‘Mérieux NutriSciences, Mérieux NutriSciences Spotlight – Sharing our expertise in an easy-to-read e-book: Environmental Monitoring, 2018.’’